Our Surface Finishing Services
Surface finishing services are often used to improve corrosion resistance, durability and part appearance.
Your one-stop machine shop for manufacturing and surface finishing services.
CNC machine metal and plastic parts for high quality and aesthetic finishes. Sandblast, anodize, powder coat and more in as soon as 7 days.
Our advantages:
- Competitive Price
- Fast turnaround
- Tolerances down to ±0.005mm
- Global Delivery
- Perfect after-sales service

Common Surface Finishing Services
Below is a list of finishes available for investment casting and CNC machining projects. If you require a custom finish please contact: quote@alliedcn.com
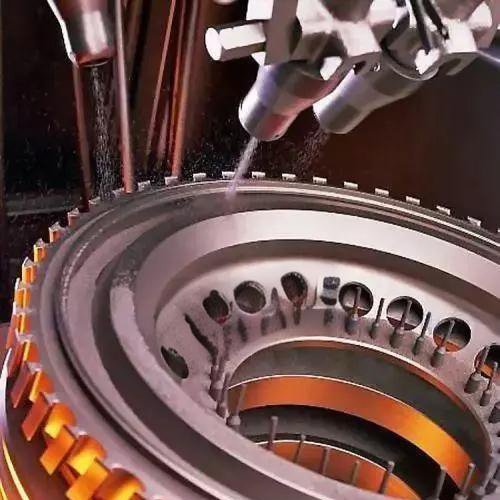

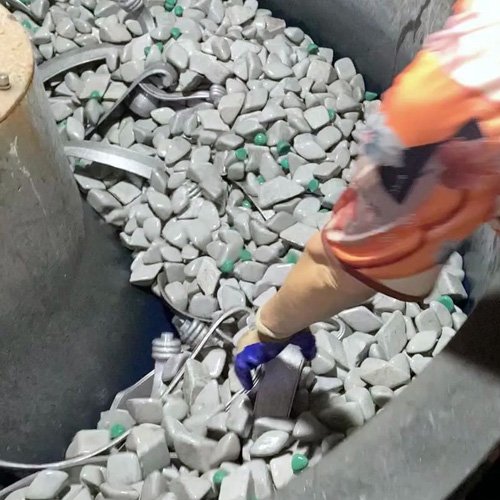
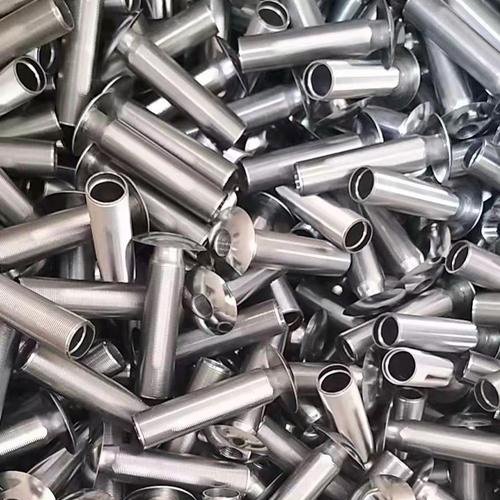
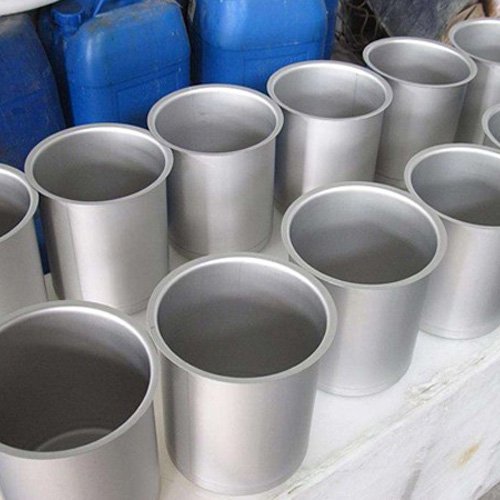

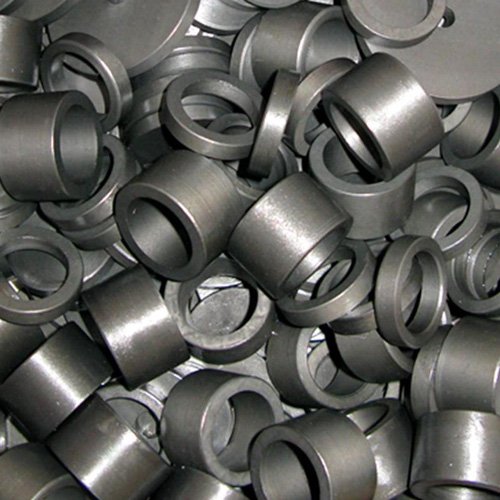

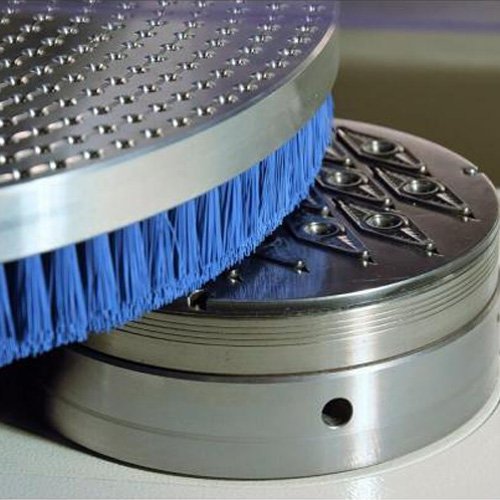
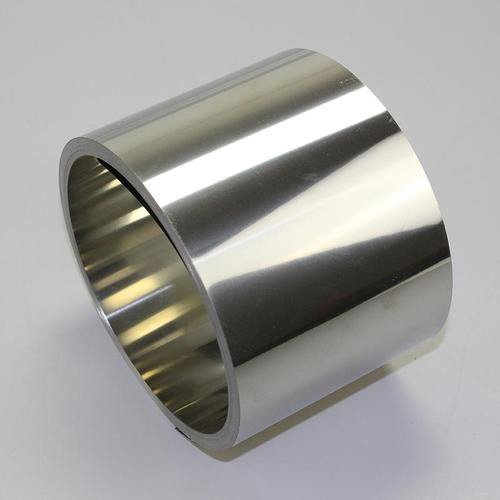
50+ Materials.
3M+ Parts Made.
20+ Years Experience.
Surface Finish Details
Delivered worldwide.
100% Quality Assurance.
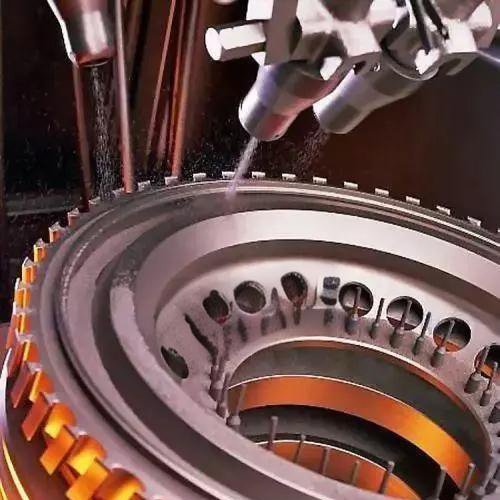
Sandblasting surface treatment:
Abrasive blasting is a finishing process where a media is propelled at a high velocity against a part’s surface to smooth or roughen it, or to remove contaminants, often in preparation for painting or another finishing process.
Although commonly referred to as sandblasting, blasting media with different abrasive properties may be used depending on the desired result. Media types include sand, metal shot, plastic or glass beads, walnut shells, baking soda, and even dry ice.
For example, machined parts are bead blasted with glass beads which results in a uniform grainy texture and reduced machining marks.
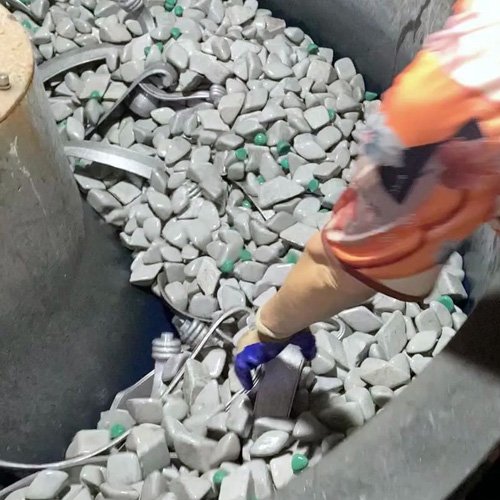
Vibratory finishing:
Vibratory finishing is an inexpensive method of cleaning, deburring, and smoothing large amounts of small parts.
It works by placing parts in a bowl filled with either ceramic or abrasive impregnated plastic media. As the bowl vibrates, the media and parts tumble, rubbing against each other creating a uniform random surface texture and slightly rounded edges.
Finish your custom parts with Allied’s finishing service.
Request a quote, or design vibratory finished parts with Allied’s FREE CAD.
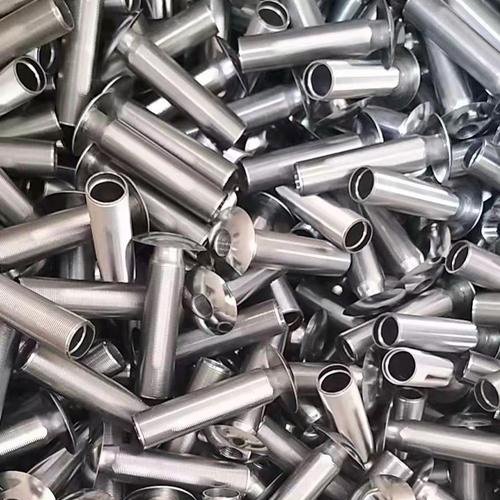
Electroplating:
Plating surface preparation services include: nickel plating, silver plating, gold plating, galvanizing, chrome plating, tin plating and more.
Plated workpieces have a smooth, lustrous surface. Not only does it reduce corrosion and improve appearance, it is also ideal for solderability and electrical conductivity.
Commonly applicable materials include: aluminum, steel, stainless steel, brass, and more.
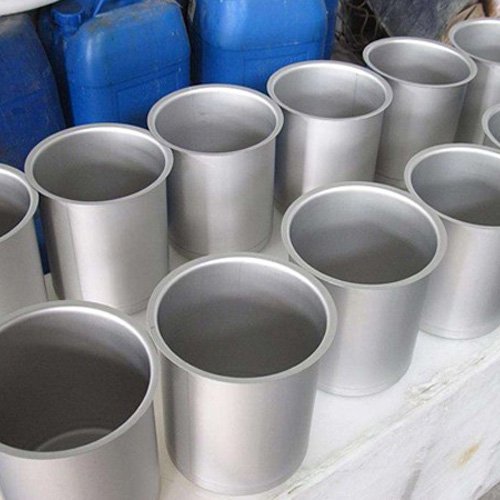
Pickling and passivation:
Acid washing is a common metal surface treatment method, mainly used to remove dirt, oxides, rust, oil and other impurities on the metal surface.
Although the metal surface finish after pickling is high, it is not corrosion resistant.
However, passivation is a corrosion-resistant treatment method, which improves the performance of the metal surface through the formation of a layer of tightly dense oxide or compound film, which is corrosion-resistant.
Since pickling provides a clean surface for passivation and ensures that the passivating agent is able to make sufficient contact with the metal surface to form a dense protective layer. Therefore, pickling is usually performed prior to passivation.

Surface polishing :
Surface polishing is a light-integrated processing method utilizing mechanical, chemical, or electrochemical action in a polishing machine or belt grinder. It can result in a smooth or mirror-gloss surface on the workpiece.
Polishing finishes are suitable for all materials, but because the diameter of the polishing wheel is typically about 6 inches, polishing may not be effective on parts with sharp, intricate, recessed, or fragile features.
Note that harder materials, such as stainless steel, take longer and are more expensive to polish than softer materials such as aluminum.
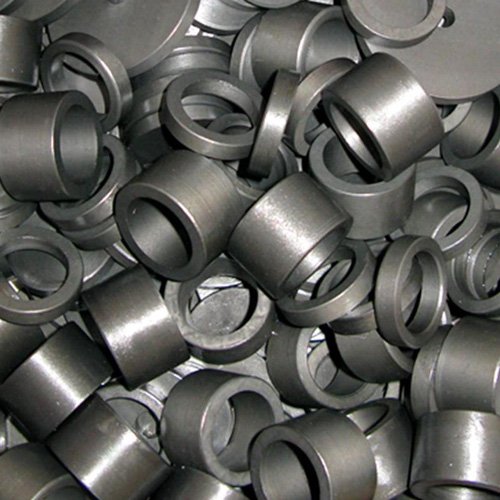
Phosphating treatment:
Phosphating is commonly used pretreatment technology, the principle belongs to the chemical conversion film treatment, mainly applied to metal surface phosphating, non-ferrous metal (such as aluminum, zinc) pieces can also apply phosphating.
Phosphate workpiece corrosion resistance, low coefficient of friction, smooth surface and longer service life.
Metal phosphate treatment process is relatively simple, easy to operate, low cost. After phosphating the metal surface can be further coated with other coatings, such as paint, coatings, plating layer.

Blackening treatment:
Black oxide, sometimes referred to as blackening, is a low-cost finishing method that increases corrosion resistance, improves wear resistance, reduces reflections and enhances the appearance of parts.
Black oxide conversion coatings are formed by dipping ferrous parts into a hot alkaline brine solution bath. Once immersed, a chemical reaction occurs on the surface of the part to form a magnetite coating. The final step is to apply an oil, wax or lacquer for added corrosion resistance.
Allied’s custom finishing services provide the ability to black oxide coat your custom parts easily.
Available Material
These are the Materials we recommend to you. Of course, we provide customized services.
Stainless steel castings area general name for castings made of various stainless steel materials (also called stainless steel investment casting).
Carbon steel is one of the main materials in the current cast steel industry. lt has the advantages of low cost, high wear resistance, easy preparation.
Alloy steel is mainly divided into two categories: low alloy steel and high alloy steel.Investment cast alloy steels are usually low alloy steels.
Factory Environment

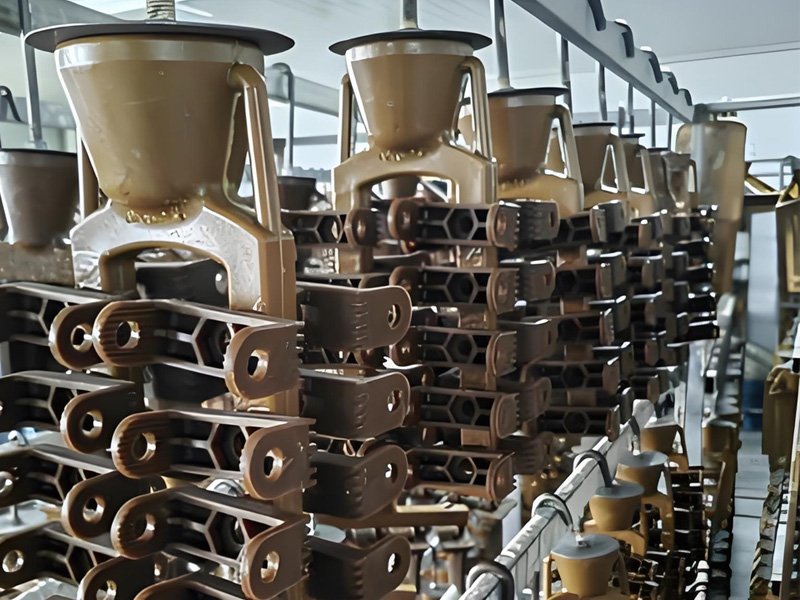
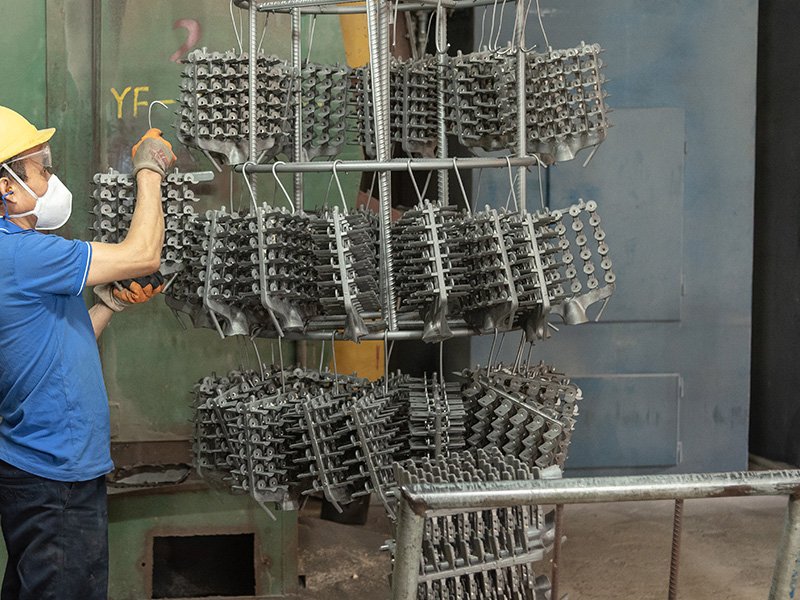


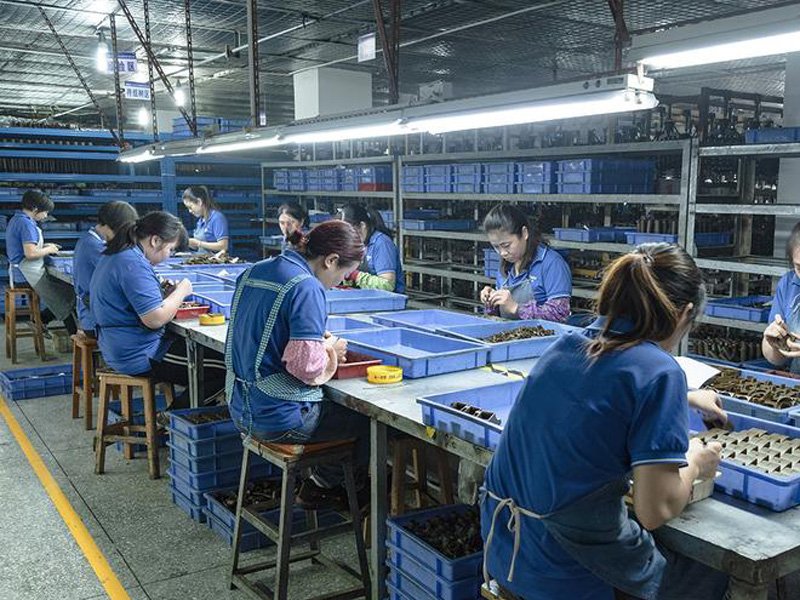
Why Choose Allied Metal as Your Business Partner ?
- Expertise: More than 20 years of experience in investment casting and CNC machining.
- Quality: Certified to ISO 9001 and TS 16949, ensuring top-tier quality management.
- Capacity: Ability to produce up to 1000 tons of high-quality castings per years.
- Technology: Equipped with an automatic shell drying line for optimal efficiency and consistency.
- Customer Focus: Dedicated to meeting the unique needs of our clients with tailored solutions and exceptional service.